Plastic extrusion for creating even, top-grade parts
Plastic extrusion for creating even, top-grade parts
Blog Article
Understanding the Basics and Applications of Plastic Extrusion in Modern Manufacturing
In the world of modern-day production, the technique of plastic extrusion plays a crucial role. Unraveling the basics of this process discloses the real flexibility and capacity of plastic extrusion.
The Basics of Plastic Extrusion Refine
While it might appear complicated, the principles of the plastic extrusion procedure are based upon fairly uncomplicated principles. It is a manufacturing process where plastic is melted and after that shaped into a continual profile through a die. The raw plastic material, usually in the form of pellets, is fed into an extruder. Inside the extruder, the plastic goes through warm and stress, causing it to melt. The molten plastic is then forced through a shaped opening, referred to as a die, to develop a long, constant product. The extruded product is cooled and afterwards cut to the preferred size. The plastic extrusion procedure is thoroughly made use of in numerous industries because of its effectiveness, flexibility, and cost-effectiveness.
Different Sorts Of Plastic Extrusion Techniques
Building upon the fundamental understanding of the plastic extrusion procedure, it is required to check out the different methods included in this manufacturing approach. In contrast, sheet extrusion produces big, flat sheets of plastic, which are usually additional processed into products such as food product packaging, shower drapes, and auto components. Recognizing these strategies is crucial to using plastic extrusion successfully in contemporary manufacturing.
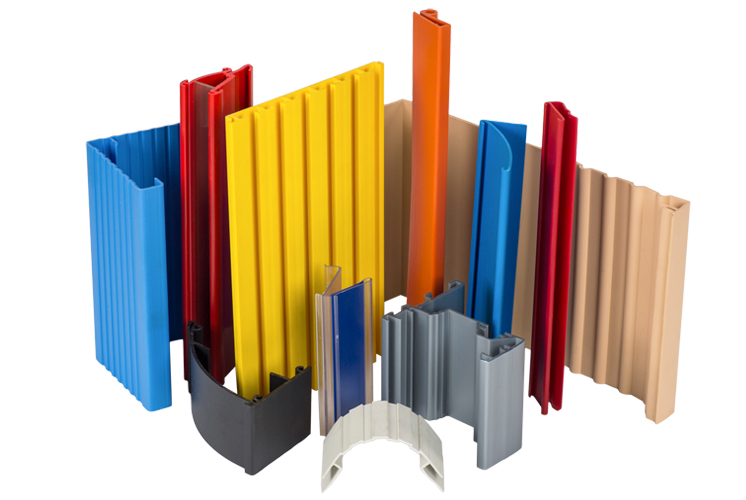
The Duty of Plastic Extrusion in the Automotive Market
An overwhelming bulk of parts in modern lorries are items of the plastic extrusion process. This procedure has revolutionized the automotive market, transforming it right into a more reliable, economical, and flexible production market. Plastic extrusion is mainly used in the production of numerous car elements such as bumpers, grills, door panels, and control panel trim. The procedure provides an attire, constant result, allowing manufacturers to produce high-volume components with great precision and minimal waste. The agility of the extruded plastic parts adds to the general decrease in lorry weight, enhancing fuel effectiveness. The durability and resistance of these components to warmth, cool, and influence improve the durability of cars. Thus, plastic extrusion plays a crucial duty in automobile manufacturing.
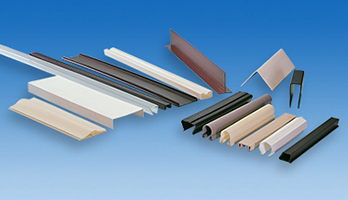
Applications of Plastic Extrusion in Consumer Item Production
Beyond its considerable effect on the automotive sector, plastic extrusion proves similarly reliable in the realm of customer goods producing. This procedure is vital in developing a broad variety of products, from food packaging to house home appliances, toys, and even clinical tools. The adaptability of plastic extrusion allows manufacturers to make and generate complicated shapes and sizes with high precision and effectiveness. Furthermore, as a result of the recyclability of many plastics, extruded elements can be recycled, lowering waste and expense. The versatility, versatility, and cost-effectiveness of plastic extrusion make it a recommended choice for numerous durable goods suppliers, adding substantially to the industry's growth and innovation. However, the ecological ramifications of this extensive usage need cautious factor to consider, a topic to be reviewed additionally in the subsequent Bonuses area.
Environmental Impact and Sustainability in Plastic Extrusion
The pervasive usage of plastic extrusion in manufacturing invites analysis of its ecological ramifications. As a my company procedure that often utilizes non-biodegradable materials, the ecological effect can be significant. Power intake, waste production, and carbon emissions are all worries. Market developments are increasing sustainability. Efficient equipment decreases power use, while waste monitoring systems reuse scrap plastic, decreasing basic material needs. In addition, the growth of eco-friendly plastics offers an extra eco-friendly choice. Despite these renovations, additionally advancement is needed to reduce the environmental impact of plastic extrusion. As society leans in the direction of sustainability, makers must adjust to remain practical, emphasizing the importance of continual research study and innovation in this area.
Conclusion
In final thought, plastic extrusion plays a critical duty in modern manufacturing, particularly in the auto and customer items markets. Understanding the fundamentals of this process is essential to enhancing its advantages and applications.
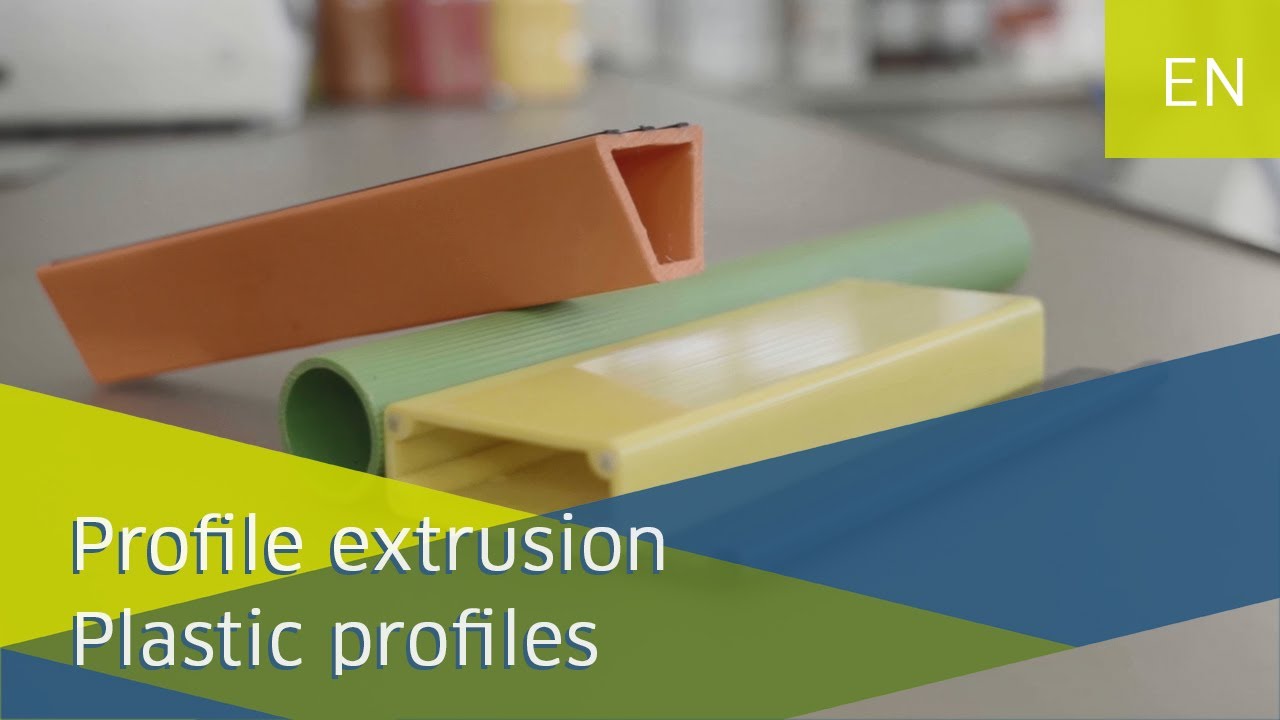
The plastic extrusion procedure is extensively used in numerous markets due to its performance, versatility, and cost-effectiveness.
Structure upon the fundamental understanding of the plastic extrusion procedure, it Get the facts is necessary to check out the numerous techniques included in this production method. plastic extrusion. In contrast, sheet extrusion produces huge, level sheets of plastic, which are normally further processed into products such as food packaging, shower curtains, and auto parts.An overwhelming majority of parts in contemporary vehicles are products of the plastic extrusion procedure
Report this page